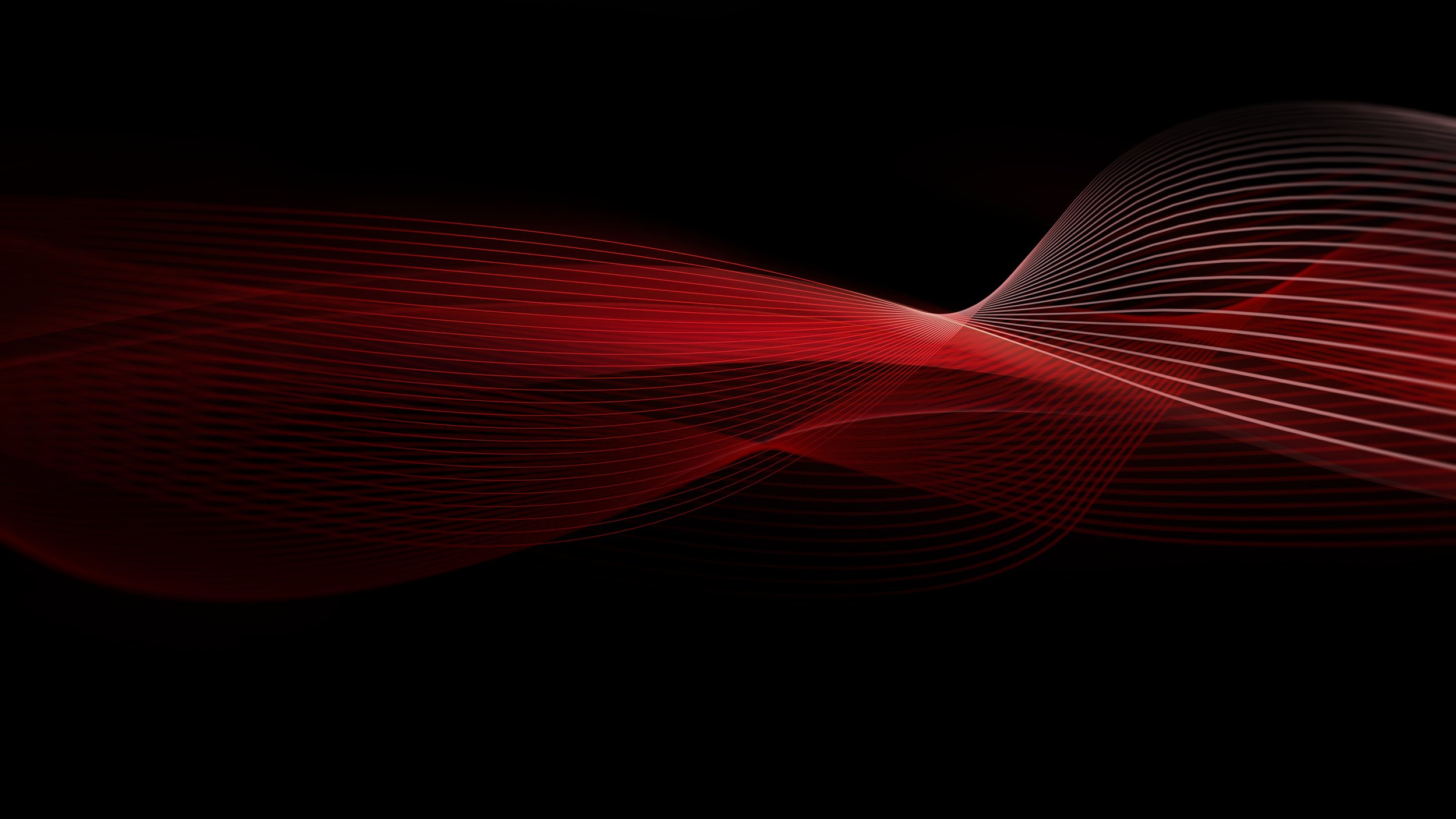
Computational Fluid Dynamics
CFD can help you evaluate, validate and optimise your system's performance prior to production, reducing product development time and testing costs and test product performance prior to production.
CFD is a computer simulation technique that allows detailed analysis of fluid flow through any product. It allows the fluid mass flow, velocity, density, temperature, pressure, concentration or any derived fluid property to be calculated at all locations within the flow field. The interaction of the fluid with its solid boundaries, such as fluid-dynamic forces and heat transfer rates can also be calculated accurately for use in stress analysis. It can be used to: calculate design mass flow rates, pressure drops and heat transfer rates together with fluid dynamic forces - lift, drag and pitching moments.
CFD can be embedded into the design process at an early stage and will help evaluate, validate and optimise your system or product prior to physical testing reducing product development time and testing costs.
Why CFD?
Rapid product development and design validation before more costly physical testing
Reduce prototype and test requirements
Comprehensive product details not limited by test instrumentation
Improved optimisation performance
Reduce costs Improve reliability and durability
CFD Methodology
Swift TG Solutions follows the following process for Computational Fluid Dynamics (CFD) analysis:
Computer Aided Design (CAD) data: the entry point for CFD simulation is CAD data, which can be supplied by the client, or by Swift TG Solutions Design consultancy.
Prepare CFD simulations: Swift TG Solutions will then define and set up physical and numerical models and impose operating conditions.
Run CFD simulations: Swift TG Solutions run the CFD simulations. Calculations are run on multi-processor machines for parallel acceleration. This is done until convergence is obtained for steady-state flows or for an allocated time for time-resolved, unsteady flows.
Produce solutions through analysis: the data from the simulations is then analysed. Through detailed investigation in 3D of the calculated data and reports on important quantities, which may be local and in real time, or time and space averaged, the main fluid and energy flow features are extracted. Graphs, flow visualisation of streamlines or velocity vector fields, and contour maps of variables such as pressure, temperature and velocity fields are also produced, tracking the evolution of these quantities during the simulations. In a gradual approach and as part of the process of deriving a solution, the choice of physical models will often be refined along with the meshing specifications during a study, starting with simpler modelling. This can then instruct further detailing, depending on the results of the analysis or as a design becomes final.
Get in Touch
If you want to create superior products efficiently and within budget, we are here to help.
With decades of experience, an impressive customer base and projects that span many industries, look no further than Swift TG Solutions for all your Computer Aided Engineering requirements.
Please contact us to discuss your needs, however big or small and whatever stage of the project you are at.